
Perawatan Prediktif Solusi Zero Downtime Mesin Industri
Dalam industri manufaktur, mesin dan peralatan produksi menjadi tulang punggung utama yang mendukung kelancaran proses produksi. Namun, kendala paling sering yang dihadapi adalah downtime mesin — saat mesin harus berhenti beroperasi karena kerusakan atau perawatan. Downtime ini bisa berdampak besar, mulai dari penurunan produktivitas hingga kerugian finansial yang signifikan. Maka dari itu, munculnya konsep perawatan prediktif sebagai solusi untuk mencapai zero downtime atau nol waktu berhenti mesin, menjadi terobosan penting yang kini banyak diterapkan oleh industri manufaktur modern.
Memahami Perawatan Prediktif
Perawatan prediktif adalah pendekatan pemeliharaan mesin yang berdasarkan pada data dan analisis kondisi mesin secara real-time atau berkala. Dibandingkan dengan perawatan tradisional seperti perawatan rutin (preventive maintenance) yang dilakukan secara berkala tanpa melihat kondisi nyata mesin, atau perawatan korektif yang dilakukan setelah kerusakan terjadi, perawatan prediktif bertujuan untuk mendeteksi tanda-tanda awal kerusakan sehingga perbaikan bisa dilakukan sebelum kerusakan benar-benar terjadi.
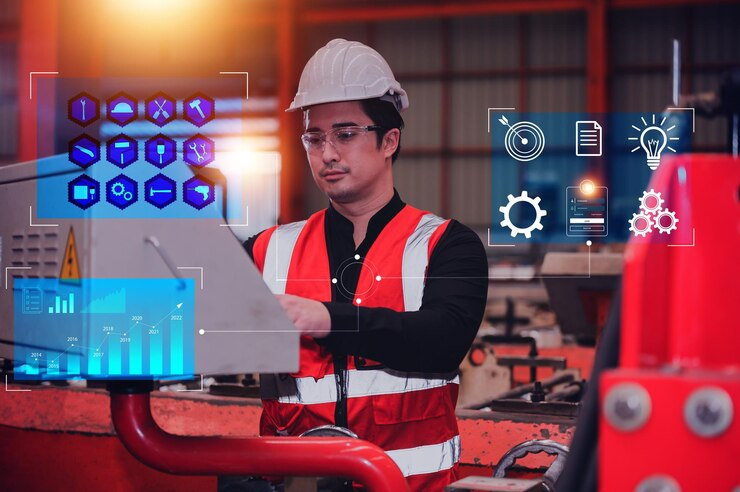
Dengan teknologi sensor, IoT (Internet of Things), dan analitik data, perawatan prediktif memungkinkan pengawasan terus-menerus terhadap kondisi mesin—seperti getaran, suhu, kebisingan, tekanan, dan lainnya. Data tersebut dianalisis menggunakan algoritma cerdas untuk memprediksi kapan dan bagian mana mesin yang perlu perhatian.
Keunggulan Perawatan Prediktif dalam Industri Manufaktur
1. Mengurangi Downtime dan Biaya Perbaikan
Dengan deteksi dini masalah, perawatan prediktif membantu menghindari kerusakan parah yang dapat menyebabkan downtime lama. Sebagai hasilnya, proses produksi dapat terus berjalan dengan lancar tanpa gangguan yang berarti. Selain itu, perbaikan yang dilakukan secara terencana dan tepat waktu umumnya lebih murah dibandingkan perbaikan besar akibat kerusakan mendadak.
2. Memperpanjang Umur Mesin
Perawatan yang dilakukan berdasarkan kondisi nyata mesin membantu menjaga performa optimal. Dengan begitu, umur teknis mesin bisa bertahan lebih lama, dan biaya investasi mesin baru dapat diundur.
3. Meningkatkan Efisiensi Produksi dan Kualitas Produk
Mesin yang dalam kondisi prima tentu mendukung proses produksi yang lebih efisien, mengurangi produk cacat akibat kerusakan alat, dan meningkatkan konsistensi kualitas produk jadi.
Implementasi Perawatan Prediktif: Teknologi dan Strategi
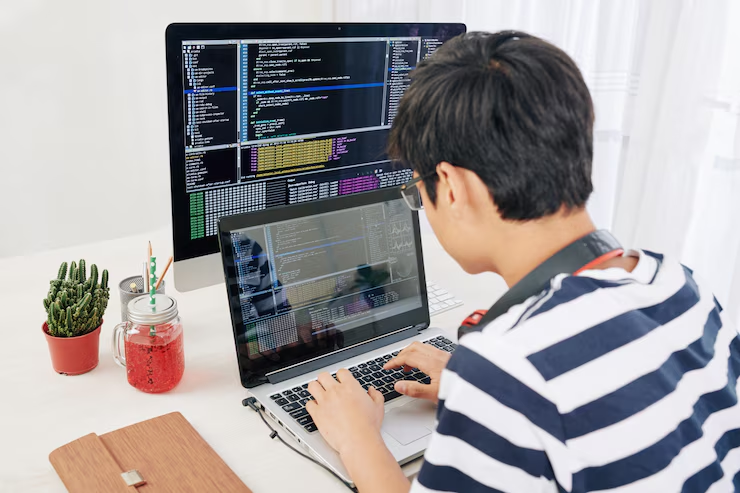
Sensor dan IoT
Pemasangan sensor di berbagai titik mesin adalah langkah awal untuk mengumpulkan data kondisi operasional mesin secara real-time. Sensor ini bisa mengukur berbagai parameter penting seperti getaran, suhu, tekanan, dan kelembaban.
Data Analytics dan AI
Data yang terkumpul dianalisis menggunakan perangkat lunak canggih yang sering melibatkan AI (Artificial Intelligence) dan machine learning. Sistem ini mendeteksi pola abnormal dan memprediksi waktu potensial terjadinya kerusakan.
Dashboard Pemantauan
Data hasil analisis biasanya disajikan dalam bentuk dashboard yang mudah dipahami oleh tim maintenance maupun manajemen. Hal ini memungkinkan pengambilan keputusan cepat dan tepat dalam penjadwalan perawatan.
Tantangan dalam Menerapkan Perawatan Prediktif
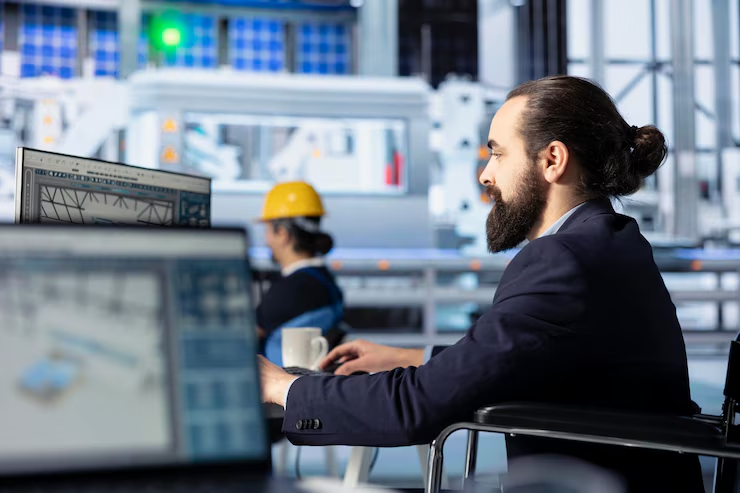
Biaya Investasi Awal
Implementasi perawatan prediktif memerlukan investasi dalam sensor, perangkat lunak, dan pelatihan sumber daya manusia. Namun, biaya ini bisa diimbangi dengan penghematan dari pengurangan downtime dan kerusakan mesin.
Kebutuhan SDM Terampil
Pengoperasian teknologi canggih memerlukan tenaga kerja yang familiar dengan IoT dan analitik data, sehingga pelatihan dan perubahan budaya kerja menjadi bagian penting.
Integrasi Sistem
Menyatukan teknologi perawatan prediktif dengan sistem produksi yang sudah ada kadang menjadi tantangan tersendiri, terutama di pabrik yang menggunakan mesin dengan teknologi lama.
Penerapan Perawatan Prediktif di Industri Manufaktur
Sebuah pabrik otomotif besar menerapkan sistem perawatan prediktif dengan memasang sensor getaran di mesin produksi utama. Melalui analisis data, mereka berhasil mendeteksi pola getaran berlebih yang menandakan keausan bearing. Dengan peringatan dini tersebut, tim maintenance dapat mengganti bearing sebelum terjadi kerusakan fatal sehingga mesin tidak mengalami downtime.
Hasilnya, pabrik mencatat penurunan downtime hingga 40% dan peningkatan efisiensi produksi sebesar 15%. Investasi di awal pun kembali dalam waktu kurang dari satu tahun.
Perawatan prediktif hadir sebagai solusi revolusioner untuk mengatasi masalah downtime mesin di industri manufaktur. Dengan memanfaatkan teknologi sensor, IoT, dan analitik data, perusahaan dapat mengidentifikasi masalah secara dini dan melakukan perawatan yang tepat waktu. Hal ini tidak hanya mengurangi biaya dan waktu berhenti mesin, tetapi juga meningkatkan umur mesin, efisiensi proses produksi, dan kualitas produk.
Meski demikian, kesuksesan penerapan perawatan prediktif memerlukan investasi di teknologi dan pengembangan sumber daya manusia yang memadai. Namun, manfaat jangka panjang yang didapat menjadikan perawatan prediktif sebagai strategi unggulan bagi industri manufaktur yang ingin tetap kompetitif dan berkelanjutan di era digital ini.
Terima kasih telah membaca. Kami di panaindustrial.com terus berkomitmen membagikan insight terkini seputar teknologi industri dan dinamika industri manufaktur yang berkembang pesat. Bersama, mari dorong kemajuan manufaktur Indonesia ke arah yang lebih inovatif dan berkelanjutan.